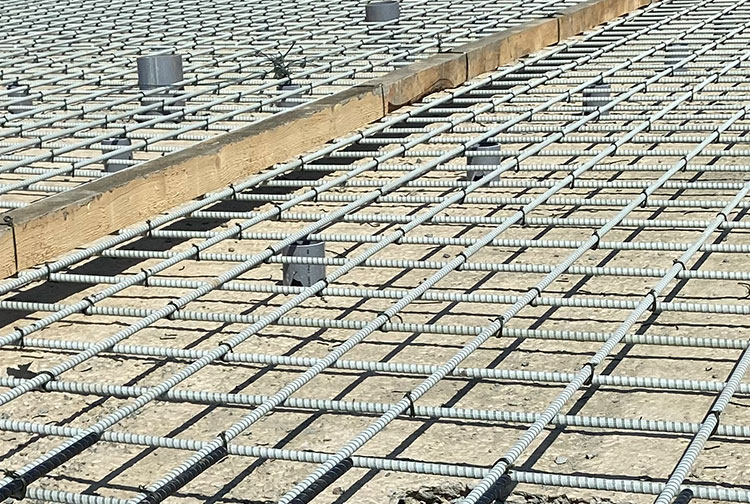
Image: FRP materials being used in a construction project.
Introduction to FRP in Construction
Fiber-Reinforced Polymer (FRP) is transforming the construction industry with its lightweight, durable, and corrosion-resistant properties. As project managers and engineers seek innovative solutions to reduce costs while maintaining structural integrity, FRP emerges as a game-changer. This article delves into the cost benefits of FRP in construction projects, comparing it with traditional materials like steel and concrete, and highlighting its long-term financial advantages.
From bridges to buildings, FRP's versatility makes it a preferred choice for modern infrastructure. By exploring its economic impact, we aim to provide insights for stakeholders looking to optimize budgets without compromising quality.
What is FRP?
FRP is a composite material made of a polymer matrix reinforced with fibers, such as glass, carbon, or aramid. Its high strength-to-weight ratio, resistance to environmental factors, and ease of installation make it ideal for construction applications. Unlike steel, FRP does not corrode, and unlike concrete, it is significantly lighter, reducing transportation and labor costs.
Cost Benefits of FRP in Construction
The adoption of FRP in construction projects offers multiple cost-saving opportunities. Below, we explore the key financial advantages in detail.
1. Reduced Material and Installation Costs
FRP components are lightweight, often weighing 50-75% less than steel or concrete. This reduces the need for heavy machinery during transportation and installation, lowering equipment rental and fuel costs. Additionally, FRP can be prefabricated, allowing for faster assembly on-site, which minimizes labor expenses.
For example, in bridge construction, FRP panels can be installed in a fraction of the time required for concrete slabs, reducing project timelines and associated costs. The table below compares the installation costs of FRP and traditional materials for a hypothetical bridge deck.
Material | Weight (kg/m²) | Installation Time (hours) | Estimated Cost ($/m²) |
---|---|---|---|
FRP | 20 | 10 | 150 |
Concrete | 240 | 24 | 250 |
Steel | 100 | 18 | 200 |
Table: Comparison of installation costs for bridge deck materials.
2. Lower Maintenance and Lifecycle Costs
One of FRP's most significant cost benefits is its resistance to corrosion, UV radiation, and chemical exposure. Unlike steel, which requires regular maintenance to prevent rust, or concrete, which may crack over time, FRP structures maintain their integrity with minimal upkeep. This translates to substantial savings over the lifespan of a project.
For instance, in coastal areas where saltwater accelerates corrosion, FRP-reinforced structures can last decades without the need for costly repairs. Studies suggest that FRP can reduce maintenance costs by up to 60% compared to traditional materials.
3. Energy Efficiency in Production and Transportation
While the initial production cost of FRP may be higher than that of concrete, its energy-efficient manufacturing processes and reduced transportation costs offset this expense. FRP's lightweight nature means fewer resources are needed to move materials to construction sites, lowering carbon emissions and fuel costs.
Moreover, advancements in FRP manufacturing have made it more cost-competitive. The use of recycled fibers and sustainable polymers further reduces production costs, aligning with the growing demand for eco-friendly construction materials.
4. Extended Service Life
FRP's durability ensures a longer service life for structures, reducing the need for replacements or major renovations. For example, FRP-reinforced concrete beams have been shown to withstand harsh environmental conditions for over 50 years, compared to 20-30 years for steel-reinforced beams. This extended lifespan directly impacts the total cost of ownership, making FRP a financially sound investment.
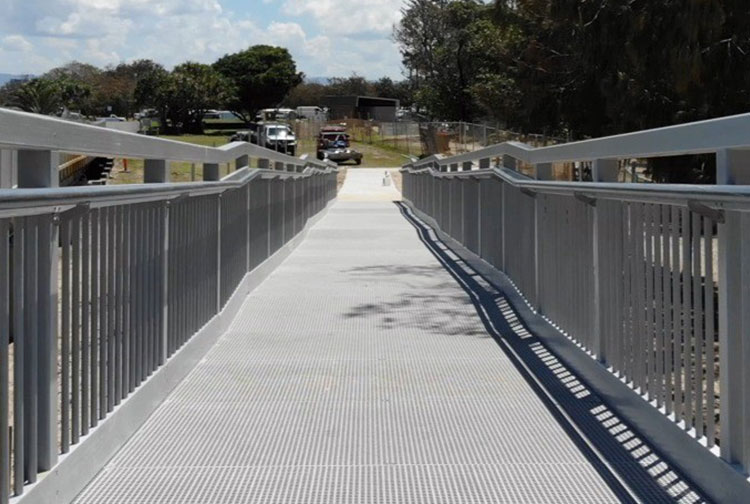
Image: A bridge constructed with FRP components, showcasing durability.
FRP vs. Traditional Materials: A Cost Comparison
To understand the financial advantages of FRP, it’s essential to compare it with traditional materials like steel and concrete. The following table highlights key cost factors for a typical construction project.
Factor | FRP | Steel | Concrete |
---|---|---|---|
Initial Material Cost | Moderate | Low | Low |
Installation Cost | Low | Moderate | High |
Maintenance Cost | Low | High | Moderate |
Lifespan (Years) | 50+ | 20-30 | 30-40 |
Total Lifecycle Cost | Low | High | Moderate |
Table: Cost comparison of FRP, steel, and concrete in construction.
Applications of FRP in Cost-Saving Projects
FRP’s cost benefits are evident across various construction applications. Here are some notable examples:
- Bridges and Highways: FRP decking and reinforcement bars reduce construction time and maintenance costs, especially in high-traffic areas.
- Buildings: FRP panels and cladding systems lower energy costs by providing excellent insulation and reducing structural weight.
- Marine Structures: FRP’s corrosion resistance makes it ideal for docks, piers, and seawalls, minimizing repair expenses in harsh environments.
- Retrofitting: FRP wraps can strengthen existing structures without the need for costly demolition, extending the life of aging infrastructure.
Challenges and Considerations
While FRP offers significant cost benefits, there are challenges to consider. The initial cost of FRP materials can be higher than that of steel or concrete, which may deter budget-conscious projects. However, this upfront investment is often offset by long-term savings in maintenance and lifecycle costs.
Additionally, the construction industry may face a learning curve when adopting FRP, as it requires specialized knowledge for design and installation. Partnering with experienced FRP suppliers and contractors can mitigate these challenges and ensure cost-effective implementation.
Case Studies: Real-World Cost Savings with FRP
Several projects demonstrate FRP’s cost-saving potential:
- Hall’s Harbor Wharf, Canada: By using FRP piles and decking, this project reduced maintenance costs by 50% compared to traditional timber and steel, with a projected lifespan of over 60 years.
- I-95 Bridge, Florida, USA: FRP reinforcement bars were used to repair a corroded bridge, saving 30% on repair costs and extending the structure’s life by 25 years.
- Commercial Building, UAE: FRP cladding reduced cooling costs by 20% due to its insulating properties, lowering operational expenses for the building owner.
Future Trends in FRP Cost Efficiency
As technology advances, the cost of FRP production is expected to decrease, making it even more competitive with traditional materials. Innovations such as automated manufacturing and the use of bio-based fibers will further enhance FRP’s affordability and sustainability.
Moreover, the growing emphasis on green building practices will drive demand for FRP, as it aligns with environmental goals by reducing energy consumption and waste. Governments and organizations are also offering incentives for sustainable construction, which could offset the initial costs of FRP adoption.
Conclusion
The cost benefits of FRP in construction projects are undeniable. From reduced installation and maintenance expenses to extended service life and energy efficiency, FRP offers a compelling alternative to traditional materials. While challenges like initial costs and industry adoption remain, the long-term financial and environmental advantages make FRP a worthy investment for forward-thinking projects.
By embracing FRP, construction professionals can achieve significant cost savings while contributing to a more sustainable future. As the industry continues to evolve, FRP is poised to become a cornerstone of cost-effective and durable construction.