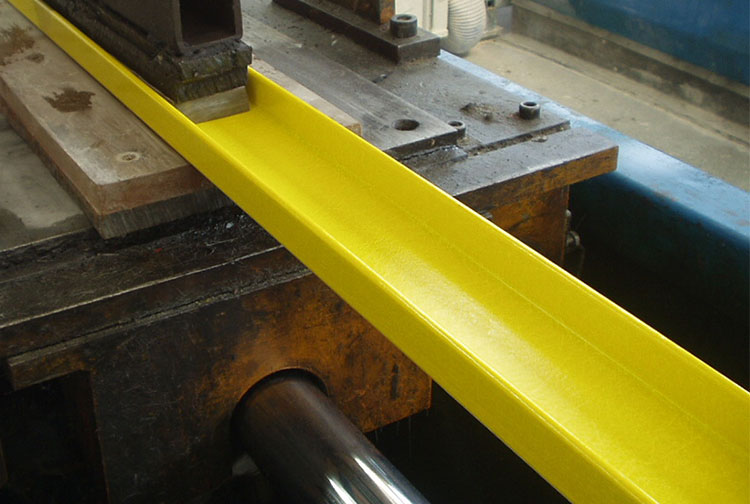
FRP C Channel
Introduction: The Battle of Materials
When it comes to structural components like C channels, the choice of material can make or break a project. Steel has long been the go-to option due to its strength and familiarity, but Fiberglass Reinforced Plastic (FRP) C channels are gaining ground as a modern alternative. So, which is the better choice—FRP C Channel or steel? In this comprehensive article, we’ll pit these two materials against each other, comparing their properties, applications, and overall value to help you make an informed decision.
C channels, named for their "C"-shaped cross-section, are widely used in construction, manufacturing, and infrastructure. While steel has dominated the market for decades, FRP—a composite material made from reinforcing fibers and a resin matrix—offers unique advantages that challenge steel’s reign. Let’s dive into the details and see how they stack up.
What Is an FRP C Channel?
An FRP C Channel is a structural profile made through the pultrusion process, where fiberglass reinforcements are impregnated with a resin (typically polyester, vinyl ester, or epoxy) and pulled through a heated die to form a solid, C-shaped component. The result is a lightweight, corrosion-resistant material with impressive strength and versatility.
FRP’s composition allows it to be tailored to specific needs, with additives like UV inhibitors or fire retardants enhancing its performance. This adaptability makes FRP C channels a favorite in industries ranging from construction to marine engineering.
What Is a Steel C Channel?
A steel C channel, on the other hand, is a metal profile formed by rolling or pressing steel into a C shape. Available in carbon steel, stainless steel, or galvanized varieties, steel C channels are renowned for their high strength and durability. They’ve been a staple in structural engineering for centuries, supporting everything from buildings to machinery.
Steel’s reliability is undeniable, but it comes with trade-offs like weight and susceptibility to rust, which can limit its use in certain environments. So, how do these two materials compare head-to-head?
FRP C Channel vs. Steel: A Detailed Comparison
Let’s break down the key factors that define the performance of FRP C channels and steel C channels: strength, weight, corrosion resistance, cost, maintenance, and more.
1. Strength and Load-Bearing Capacity
Steel: Steel C channels are incredibly strong, with a high tensile strength that makes them ideal for heavy-duty applications. They can support massive loads, which is why they’re common in skyscrapers, bridges, and industrial frameworks.
FRP: FRP C channels also boast impressive strength, particularly when reinforced with fiberglass or carbon fiber. While they may not match steel’s raw tensile strength, their strength-to-weight ratio is exceptional, making them suitable for many structural tasks without the bulk.
Verdict: Steel wins for absolute strength, but FRP holds its own for applications where weight is a concern.
2. Weight
Steel: Steel is heavy—there’s no getting around it. A steel C channel’s density can complicate transportation, installation, and structural design, especially in projects requiring lightweight materials.
FRP: FRP C channels are significantly lighter, often weighing 75% less than steel equivalents. This makes them easier to handle, reduces shipping costs, and allows for innovative designs in weight-sensitive applications like aerospace or portable structures.
Verdict: FRP takes the lead for its lightweight advantage.
3. Corrosion Resistance
Steel: Steel is prone to rust and corrosion, especially in humid, salty, or acidic environments. While stainless steel and galvanized coatings improve resistance, they increase costs and don’t eliminate the issue entirely.
FRP: FRP C channels are inherently corrosion-resistant, thanks to their non-metallic composition. They thrive in harsh conditions—think coastal areas, chemical plants, or wastewater facilities—without degrading.
Verdict: FRP is the clear winner for corrosion resistance.
4. Cost
Steel: Steel C channels are generally cheaper upfront, with a well-established supply chain keeping costs predictable. However, long-term expenses like maintenance and corrosion protection can add up.
FRP: FRP C channels often have a higher initial cost due to the manufacturing process and raw materials. Over time, though, their durability and low maintenance needs can make them more cost-effective.
Verdict: Steel is cheaper initially, but FRP may save money in the long run.
5. Maintenance
Steel: Steel requires regular maintenance—painting, coating, or replacing rusted sections—to maintain its integrity. This can be a significant burden in large-scale projects.
FRP: FRP C channels are virtually maintenance-free. They resist weathering, UV damage, and corrosion without needing protective treatments.
Verdict: FRP excels in low-maintenance performance.
6. Thermal and Electrical Conductivity
Steel: Steel conducts heat and electricity, which can be a drawback in applications like electrical enclosures or climates with extreme temperature swings.
FRP: FRP is a natural insulator, offering low thermal and electrical conductivity. This makes it ideal for utility poles, electrical supports, and energy-efficient designs.
Verdict: FRP is superior for insulation properties.
7. Design Flexibility
Steel: Steel C channels are limited to standard sizes and shapes, though custom fabrication is possible at a higher cost.
FRP: The pultrusion process allows FRP C channels to be customized in shape, size, and even color, offering greater design freedom.
Verdict: FRP wins for flexibility and customization.
Comparison Table: FRP C Channel vs. Steel C Channel
Property | FRP C Channel | Steel C Channel |
---|---|---|
Strength | High (relative to weight) | Very High |
Weight | Light | Heavy |
Corrosion Resistance | Excellent | Poor (unless treated) |
Initial Cost | Higher | Lower |
Maintenance | Low | High |
Conductivity | Non-conductive | Conductive |
Design Flexibility | High | Moderate |
Applications: Where Each Material Shines
Steel C Channels: Steel excels in heavy industrial settings where maximum load-bearing capacity is non-negotiable. Think large-scale bridges, factory frameworks, or high-rise buildings. Its robustness makes it a staple in traditional construction.
FRP C Channels: FRP shines in environments where corrosion, weight, or insulation is a concern. Common uses include:
- Marine: Docks and piers exposed to saltwater.
- Chemical Plants: Structures resisting corrosive substances.
- Transportation: Lightweight railings or vehicle components.
- Utilities: Non-conductive supports for power lines.
Environmental Impact
Steel: Steel production is energy-intensive and generates significant carbon emissions. However, it’s highly recyclable, which offsets some environmental concerns.
FRP: FRP manufacturing has a lower energy footprint, and its longevity reduces replacement needs. Recycling is more challenging, though advancements are being made.
Verdict: Steel has an edge in recyclability, but FRP’s durability offers long-term sustainability.
Which Is the Better Choice?
The “better” choice between FRP C channels and steel C channels depends on your project’s specific needs:
- Choose Steel If: You need maximum strength, have a tight budget upfront, and can manage corrosion through coatings or maintenance.
- Choose FRP If: You prioritize weight savings, corrosion resistance, insulation, or low maintenance, and are willing to invest in a material with long-term benefits.
For traditional heavy-duty projects, steel remains king. But for innovative, corrosion-prone, or lightweight applications, FRP C channels often come out on top.
Conclusion
The debate between FRP C channels and steel C channels isn’t about one being universally superior—it’s about finding the right fit. Steel offers unmatched strength and affordability, while FRP brings lightweight durability and resistance to the table. By weighing factors like environment, cost, and performance requirements, you can determine which material aligns with your goals.
Whether you’re building a bridge, a chemical facility, or a lightweight structure, both FRP and steel have their place. The key is understanding their strengths and limitations to make a choice that ensures success.