
Caption: FRP pipes from top manufacturers deliver corrosion-free performance.
Introduction: The Rise of FRP Innovators
Corrosion is the Achilles’ heel of traditional materials like steel and iron, costing industries billions in repairs and replacements. But a new breed of innovators is changing the game: FRP manufacturers. Specializing in Fiberglass Reinforced Plastic (FRP), these companies are unveiling solutions that promise durability without the rust. In this article, we dive into the world of FRP manufacturers, revealing the leaders who are pioneering corrosion-free solutions for construction, marine, and industrial applications.
Why does this matter? Because FRP manufacturers aren’t just making products—they’re revolutionizing how we build and maintain infrastructure. Lightweight, strong, and immune to corrosion, their offerings are reshaping industries worldwide. Whether you’re a contractor, engineer, or business owner, understanding who these leaders are and what they bring to the table could redefine your next project. Let’s unveil the trailblazers and explore their corrosion-free legacy.
What Is FRP and Who Are the Manufacturers?
FRP stands for Fiberglass Reinforced Plastic, a composite material made by embedding glass fibers into a plastic resin matrix—typically polyester, epoxy, or vinyl ester. The result is a material that’s lightweight, incredibly strong, and resistant to environmental degradation. Unlike steel, which rusts, or wood, which rots, FRP thrives in harsh conditions, making it a go-to choice for pipes, panels, railings, and more.
FRP manufacturers are the masterminds behind this innovation. These companies design, produce, and supply FRP products, tailoring them to meet specific needs—be it corrosion resistance for marine environments or lightweight strength for construction. From global giants to specialized firms, these manufacturers are the backbone of the FRP revolution, and they’re leading the charge in corrosion-free solutions.
Why FRP Manufacturers Lead in Corrosion-Free Solutions
Corrosion isn’t just a problem—it’s a crisis. Steel pipes fail in wastewater systems, iron railings crumble by the sea, and maintenance costs skyrocket. FRP manufacturers have stepped up with a solution: Fiberglass Reinforced Plastic that defies rust. Here’s why they’re the leaders:
1. Corrosion Resistance: The Core Advantage
The hallmark of FRP is its immunity to corrosion. Steel rusts when exposed to moisture, salt, or acids, weakening structures within 20-30 years in harsh settings. FRP manufacturers produce products that laugh at these conditions. Glass fibers don’t corrode, and the plastic resin seals them tight, ensuring longevity—up to 50-100 years in aggressive environments like coastal zones or chemical plants.
Imagine a seaside dock: a steel frame might need replacing in a decade, while an FRP version from a top manufacturer stands firm for generations. This corrosion-free edge is why FRP manufacturers are unveiled as leaders—they solve a problem traditional materials can’t.
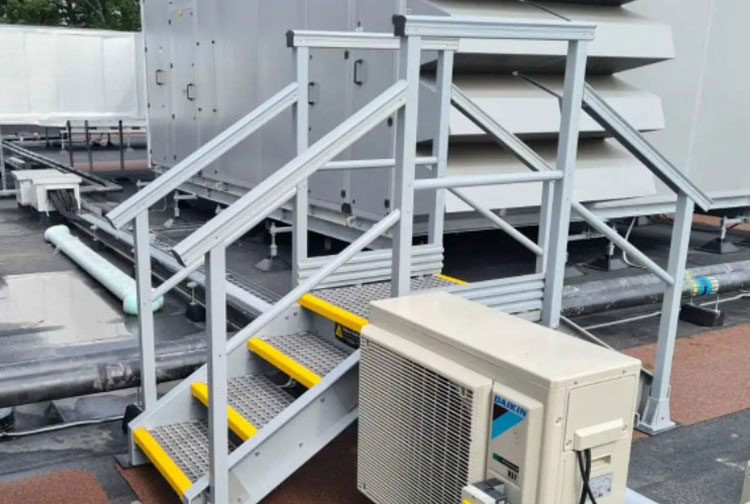
Caption: FRP railings from leading manufacturers outlast steel by the sea.
2. Lightweight Strength: Efficiency Redefined
Steel is strong but heavy—490 pounds per cubic foot—making it a logistical nightmare for transport and installation. FRP manufacturers counter with products weighing just 1-2 pounds per foot, yet boasting tensile strength of 70,000-100,000 psi, often surpassing steel’s 50,000-70,000 psi. This lightweight durability cuts shipping costs and speeds up construction.
For example, an FRP pipe from a leading manufacturer can be installed by hand in a water system, while steel demands cranes and crews. This efficiency makes FRP a practical, corrosion-free solution for modern projects.
3. Customization: Tailored Solutions
What sets FRP manufacturers apart is their ability to customize. Need a pipe resistant to acidic wastewater? They’ll tweak the resin. Want a railing that’s UV-stable for a sunny coast? They’ll adjust the fibers. From diameters to colors to strength profiles, FRP products are engineered to fit specific needs—something steel can’t match with its rigid production.
This versatility ensures corrosion-free performance across industries, cementing these manufacturers as leaders in innovative solutions.
FRP vs. Steel: The Stats Showdown
How do FRP products from these manufacturers compare to steel? Here’s the data:
Property | FRP (Fiberglass Reinforced Plastic) | Steel |
---|---|---|
Corrosion Resistance | Excellent | Poor (rusts) |
Weight | Light (1-2 lbs/ft) | Heavy (10-15 lbs/ft) |
Tensile Strength | High (70,000-100,000 psi) | Good (50,000-70,000 psi) |
Maintenance | Low | High |
Lifespan | 50-100 years | 20-50 years |
Note: Values vary by specific products and conditions.
FRP from top manufacturers outperforms steel in corrosion resistance, weight, and maintenance, making it the clear leader for corrosion-free applications.
Applications: Where FRP Manufacturers Shine
These FRP manufacturers are transforming industries with their products:
- Construction: FRP rebar and beams resist rust in bridges and buildings.
- Marine: Railings and pipes endure saltwater without corroding.
- Industrial: Tanks and ducts handle chemicals steel can’t.
- Infrastructure: Water and wastewater pipes last decades.
A coastal wastewater system, for instance, might see steel pipes fail in 15 years, while FRP pipes from a leading manufacturer keep flowing for 75. This real-world impact underscores their leadership in corrosion-free solutions.
Cost and Value: The Long-Term Win
Steel might be cheaper upfront—$500-$800 per ton vs. FRP’s $1,000-$2,000—but the math shifts over time. Steel’s rust means coatings, repairs, or replacements, costing $50-$100 per unit yearly in harsh conditions. FRP manufacturers offer products that need no such upkeep, cutting lifecycle costs by 20-40%. Their lightweight design also saves on installation, making FRP a cost-effective leader in the long run.
Sustainability: A Green Edge
Many FRP manufacturers are going green, using recycled glass fibers or eco-friendly resins. Steel production is carbon-heavy, but FRP’s durability reduces replacement frequency, lowering environmental impact. This sustainable twist enhances their leadership in corrosion-free solutions.
Challenges: Where They Face Hurdles
FRP isn’t flawless. Higher initial costs can deter small projects, and extreme heat (above 200°C) requires special resins. Steel’s raw compressive strength still wins in some heavy-load scenarios, but for corrosion-prone applications, FRP manufacturers remain unrivaled.
Conclusion: Leaders Unveiled
FRP manufacturers unveiled as leaders in corrosion-free solutions are more than suppliers—they’re innovators. With Fiberglass Reinforced Plastic, they deliver products that resist rust, lighten loads, and last generations, outpacing steel in modern demands. From marine docks to industrial pipes, these pioneers are building a corrosion-free future.
Why do they lead? Because in a world where corrosion costs time and money, FRP manufacturers offer answers. Ready to tap into their solutions? Explore these leaders and see how FRP can transform your next project!