FRP molding is a process of forming FRP products from a mold. There are a variety of FRP molding processes available, each with its own advantages and disadvantages. The right FRP molding process for a particular application will depend on a number of factors, including the shape and size of the product, the desired properties of the product, and the volume of production.
Here are some of the most common FRP molding processes:
Hand lay-up: This is the simplest and most basic FRP molding process. It involves manually placing layers of fiberglass reinforcement and resin into a mold. Hand lay-up is a good choice for small, simple products or for prototypes.
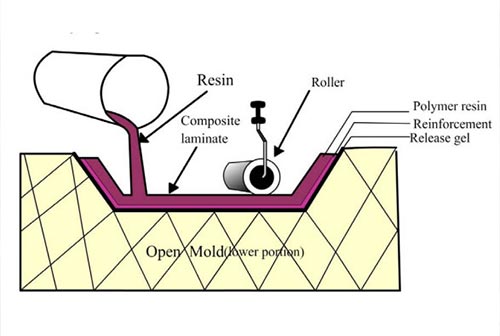
Hand layup FRP molding
Compression molding: This process involves placing fiberglass reinforcement and resin into a heated mold and then applying pressure to the mold. Compression molding is a good choice for products with complex shapes or for products that require high strength and stiffness.
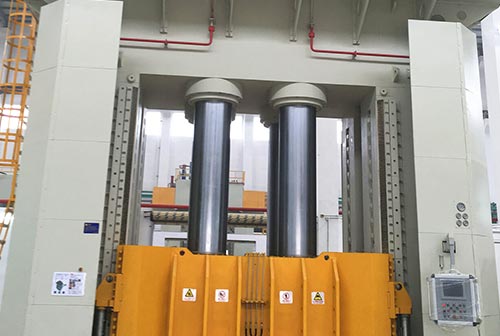
Compression molding FRP molding
Vacuum infusion molding: This process involves placing fiberglass reinforcement into a mold and then vacuuming out the air. Resin is then injected into the mold under pressure. Vacuum infusion molding is a good choice for products with complex shapes or for products that require high strength and stiffness.
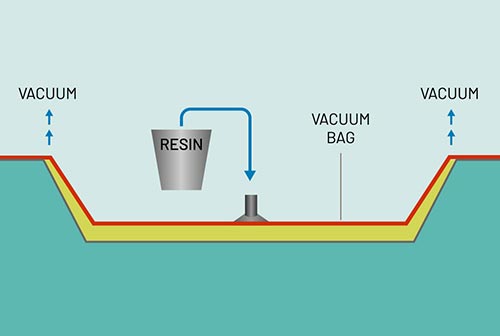
Vacuum infusion molding FRP molding
Pultrusion: This process involves pulling fiberglass reinforcement through a resin bath. The resin then cures, forming a continuous, reinforced composite. Pultrusion is a good choice for long, thin products, such as pipes and rods.
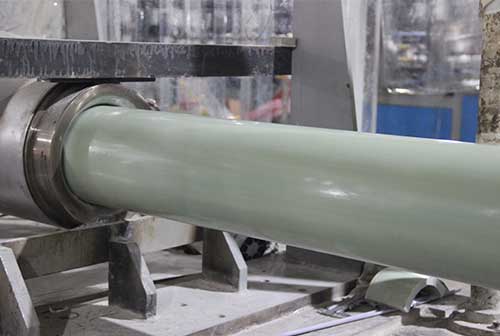
Pultrusion FRP molding
When choosing an FRP molding process, it is important to consider the following factors:
Shape and size of the product: Some FRP molding processes are better suited for certain shapes and sizes of products than others. For example, hand lay-up is a good choice for small, simple products, while compression molding is a good choice for products with complex shapes.
Desired properties of the product: Some FRP molding processes can produce products with specific properties, such as high strength, stiffness, or corrosion resistance. For example, vacuum infusion molding can be used to produce products with high strength and stiffness.
Volume of production: Some FRP molding processes are more efficient than others for high-volume production. For example, pultrusion is a good choice for high-volume production of long, thin products.
Henan Zhongsheng can help you choose the right FRP molding process for your application. We have extensive experience in a variety of FRP molding processes and can help you select the process that best meets your needs.