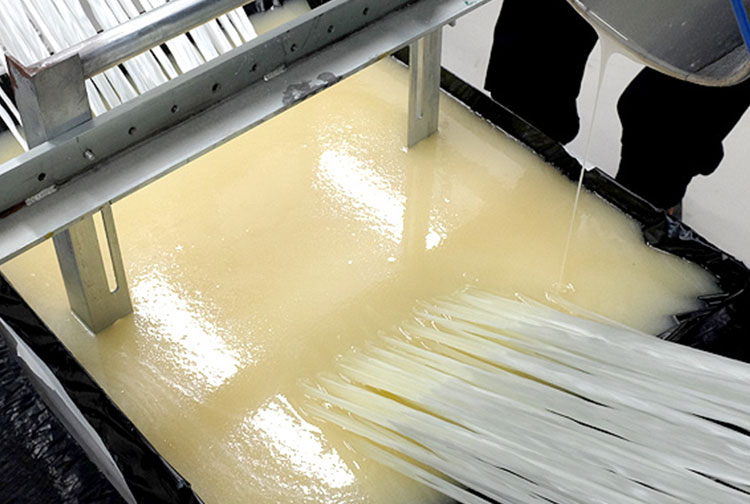
FRP Pultrusion Process
Surface bubbling is a common defect encountered in the FRP pultrusion process, leading to a reduction in the aesthetic appeal and structural integrity of the final product. Understanding the root causes of this issue is crucial for manufacturers aiming to produce high-quality pultruded profiles. This article explores the primary reasons behind surface bubbling in FRP pultrusion and provides practical solutions to mitigate this defect.
Understanding the FRP Pultrusion Process
FRP pultrusion is a continuous manufacturing process that involves pulling reinforced fibers through a resin bath, shaping them into a desired profile, and curing them to create a composite material. The process involves several steps, including:
Resin impregnation: The reinforcing fibers are thoroughly impregnated with a resin system.
Shaping: The impregnated fibers are pulled through a shaping die to form the desired profile.
Curing: The shaped profile is cured in an oven to solidify the resin and create a strong composite material.
Common Causes of Surface Bubbling
Several factors can contribute to the formation of surface bubbles during the FRP pultrusion process:
Excessive Resin: An excess amount of resin can trap air bubbles within the composite, leading to surface bubbling.
High Resin Viscosity: High resin viscosity can hinder the escape of air bubbles, resulting in their entrapment within the composite.
Improper Fiber Distribution: Uneven distribution of fibers can create voids within the composite, which can become trapped air pockets and lead to surface bubbling.
Insufficient Vacuum: Inadequate vacuum during the impregnation process can allow air to become trapped within the composite.
Rapid Curing: Rapid curing can cause the resin to solidify before trapped air has a chance to escape, resulting in surface bubbles.
Mold Design Flaws: Defects in the mold design, such as sharp corners or insufficient draft angles, can trap air and contribute to surface bubbling.
Solutions to Mitigate Surface Bubbling
Optimize Resin Formulation: Adjust the resin formulation to reduce viscosity and improve flow properties, allowing trapped air to escape more easily.
Control Fiber Content: Maintain a consistent and optimal fiber content to prevent voids and ensure proper impregnation.
Improve Vacuum Application: Enhance the vacuum system to effectively remove air from the impregnated fibers before shaping.
Optimize Curing Cycle: Adjust the curing cycle to allow sufficient time for trapped air to escape before the resin solidifies.
Refine Mold Design: Ensure that the mold design is free of defects that could trap air and contribute to surface bubbling.
Implement Quality Control Measures: Conduct regular inspections of the pultruded profiles to identify and address any quality issues.
Additional Tips for Preventing Surface Bubbling
Use Degassed Resin: Degas the resin before use to remove any dissolved air.
Maintain Consistent Processing Conditions: Ensure that process parameters such as temperature, pressure, and pull rate are consistent to minimize variations in the final product.
Regularly Clean and Maintain Equipment: Keep the pultrusion equipment clean and well-maintained to prevent contamination and ensure optimal performance.
Conclusion
Surface bubbling in FRP pultrusion can be a significant quality issue, impacting the appearance and performance of the final product. By understanding the underlying causes and implementing appropriate solutions, manufacturers can effectively mitigate this defect and produce high-quality pultruded profiles. By optimizing resin formulation, improving vacuum application, and refining mold design, it is possible to achieve a smooth and defect-free surface finish.