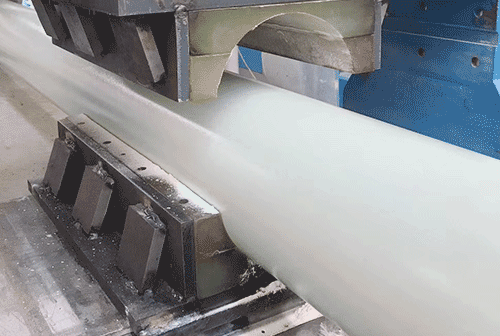
Pultrusion Process
Delve into the world of pultrusion, a continuous manufacturing process for producing fiber-reinforced plastics with a constant cross-section. Discover how this versatile technique transforms raw materials into high-performance composites, offering a unique blend of strength, durability, and lightweight properties.
Introduction:
In the realm of materials science and manufacturing, the pultrusion process stands as a testament to human ingenuity. This continuous manufacturing technique has revolutionized the production of fiber-reinforced plastics (FRPs), offering a cost-effective and efficient method for creating composites with exceptional strength, durability, and lightweight properties. Let's embark on a journey to unravel the intricacies of pultrusion, exploring its principles, applications, and the remarkable characteristics of the products it produces.
Understanding the Pultrusion Process:
At the heart of pultrusion lies a continuous process that seamlessly transforms raw materials into FRP products with a constant cross-section. This process can be broken down into several key stages:
1- Material Preparation: Reinforcing fibers, typically glass, carbon, or aramid, are carefully prepared and aligned in the desired direction.
2- Resin Impregnation: The fibers are saturated with a liquid resin matrix, ensuring complete adhesion and bonding.
3- Pulling and Shaping: The impregnated fiber bundle is pulled through a heated die, which shapes it into the desired cross-sectional profile.
4- Curing and Polymerization: As the material passes through the die, the resin undergoes curing or polymerization, solidifying the composite structure.
5- Cutting and Finishing: The cured FRP product is cut to the desired length and subjected to finishing processes, such as sanding or painting.
Properties of Pultruded FRP Products:
Pultrusion imparts unique properties to the resulting FRP products, making them highly sought-after in various applications:
1- High Strength-to-Weight Ratio: Pultruded FRPs exhibit exceptional strength and stiffness while maintaining a lightweight nature, making them ideal for weight-critical applications.
2- Durability and Corrosion Resistance: The inherent properties of the reinforcing fibers and resin matrix provide exceptional resistance to corrosion, chemicals, and harsh environments.
3- Dimensional Stability: Pultruded FRPs maintain their shape and dimensions even under extreme conditions, ensuring long-term stability and performance.
4- Design Flexibility: Pultrusion allows for the creation of a wide range of cross-sectional profiles, catering to diverse design requirements.
5- Cost-Effective Manufacturing: The continuous nature of pultrusion offers efficient and cost-effective production, especially for high-volume applications.
Applications of Pultruded FRP Products:
The versatility and exceptional properties of pultruded FRP products have led to their widespread adoption across various industries:
1- Construction and Infrastructure: Pultruded FRPs are used for reinforcing beams, columns, pipes, and other structural components in buildings, bridges, and infrastructure projects.
2- Transportation: Pultruded FRPs find applications in aircraft components, automotive parts, mass transit systems, and marine structures.
3- Energy and Utilities: Pultruded FRPs are employed in power transmission lines, wind turbine blades, and electrical insulation components.
4- Industrial and Chemical Processing: Pultruded FRPs are used for building tanks, pipes, valves, and other components in harsh industrial and chemical environments.
5- Recreational and Sporting Goods: Pultruded FRPs are utilized in golf shafts, fishing rods, hockey sticks, and other sporting goods due to their strength and lightweight properties.
Conclusion:
The pultrusion process stands as a remarkable testament to human innovation, transforming raw materials into high-performance composites with exceptional properties. Pultruded FRP products have revolutionized a wide range of industries, offering a unique blend of strength, durability, lightweight construction, and design flexibility. As the demand for high-performance materials continues to grow, pultrusion is poised to play an even more prominent role in shaping the future of manufacturing and engineering.
Additional Considerations:
1- Material Selection: The choice of reinforcing fibers and resin matrix depends on the specific application and desired properties of the pultruded product.
2- Process Control: Precise control of pultrusion parameters, such as pulling speed, resin viscosity, and curing temperature, is crucial for achieving consistent product quality.
3- Design Optimization: Careful design of pultruded components ensures optimal performance and maximizes the benefits of the material's properties.