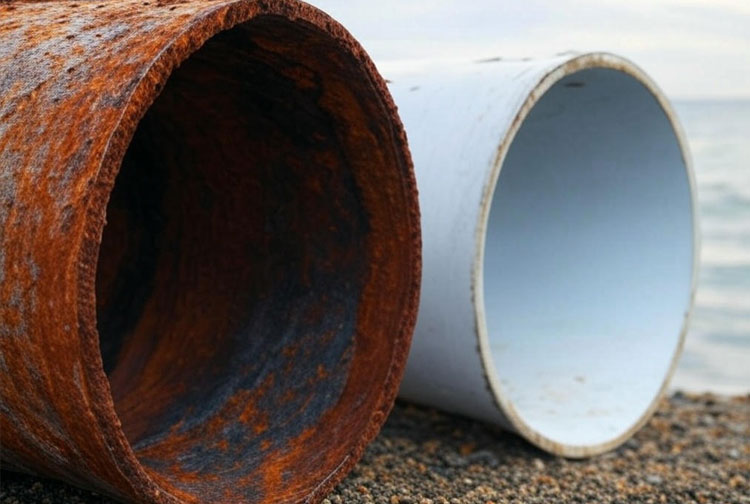
Caption: FRP composites resist corrosion where steel succumbs.
Introduction: A Material Showdown for the Ages
Steel has long been the king of construction materials, a symbol of strength and reliability that’s built skyscrapers, bridges, and factories. But a new contender is challenging its throne: FRP composites, or Fiber Reinforced Polymer composites. These innovative materials are gaining ground, and for good reason. In the battle of FRP composites vs. steel, composites are increasingly coming out on top, offering advantages that steel struggles to match. This article dives into why FRP composites are rewriting the rules of modern construction.
From corrosion resistance to lightweight design, FRP composites bring a fresh perspective to an industry ready for change. Whether you’re an architect, engineer, or builder, understanding why composites outperform steel could shape your next project. Let’s explore the key reasons FRP composites are taking the lead—and why they’re here to stay.
What Are FRP Composites and Steel?
Before we crown a winner, let’s meet the contenders. Steel is an alloy of iron and carbon, often enhanced with other elements like chromium for stainless varieties. It’s heavy, strong, and ubiquitous in construction, used in beams, rebar, and tubing. Its reputation is built on raw power, but it’s not without flaws.
FRP composites, or Fiber Reinforced Polymers, are a different beast. They combine a polymer matrix—like polyester, epoxy, or vinyl ester—with reinforcing fibers such as glass (GFRP), carbon (CFRP), or basalt (BFRP). Available as sheets, bars, or tubes, FRP composites are engineered for specific traits: lightweight, durable, and resistant to environmental wear. With the players defined, let’s see why composites come out on top.
Reason 1: Corrosion Resistance—Steel’s Fatal Flaw
Corrosion is steel’s kryptonite. When exposed to moisture, salt, or chemicals, steel rusts, weakening structures and driving up maintenance costs. In coastal areas or industrial settings, a steel beam might need replacement within 20-30 years as rust eats away at its core. Even protective coatings like galvanization only delay the inevitable, requiring regular reapplication.
FRP composites, on the other hand, laugh at corrosion. Because they’re non-metallic, Fiber Reinforced Polymers don’t rust, rot, or degrade in harsh conditions. Studies suggest FRP can last 50-100 years in aggressive environments—think marine docks or chemical plants—without losing strength. In the battle of FRP composites vs. steel, composites win hands down for longevity in corrosive settings.
Reason 2: Lightweight Strength—Less Is More
Steel is strong, no doubt—its tensile strength can hit 50,000-70,000 psi—but it’s heavy, weighing around 490 pounds per cubic foot. This bulk means higher transportation costs, bigger cranes, and more labor to install. For a skyscraper or bridge, that weight adds up fast, complicating logistics and budgets.
FRP composites flip the script with a killer strength-to-weight ratio. Depending on the fiber (e.g., carbon or glass), FRP can match or exceed steel’s tensile strength—up to 100,000 psi—while weighing just 20-25% as much. A composite beam might weigh 1-2 pounds per foot compared to steel’s 10-15. This lightweight power makes FRP easier to handle, faster to install, and ideal for projects where reducing structural load is key, like seismic retrofits or elevated platforms.
Reason 3: Low Maintenance—Set It and Forget It
Steel demands constant care. Rust-proofing, painting, and inspections are par for the course, especially in wet or salty climates. A steel bridge might need recoating every 5-10 years, with labor and material costs piling up. Miss a maintenance cycle, and you’re risking structural failure.
FRP composites are the opposite—they’re practically maintenance-free. Their corrosion resistance eliminates the need for protective treatments, and they shrug off UV rays, chemicals, and weathering. Once installed, FRP can go decades without intervention, saving time and money. In the long game of FRP composites vs. steel, composites win for hassle-free durability.
Reason 4: Cost Efficiency—Beyond the Sticker Price
Steel’s upfront cost is tempting—$500-$800 per ton versus FRP’s $1,000-$2,000 per unit. But look at the lifecycle, and the picture changes. Steel’s maintenance and replacement costs soar over time, while FRP’s initial investment pays off with minimal upkeep and a longer lifespan. For a 50-year project, FRP could slash total costs by 20-30% compared to steel in corrosive environments.
Add in installation savings—FRP’s light weight cuts labor and equipment needs—and composites become a budget-friendly choice. Steel might win the short-term price war, but FRP takes the victory in long-term value.
FRP Composites vs. Steel: The Stats Tell the Story
Numbers don’t lie. Here’s how FRP composites stack up against steel:
Property | FRP Composites | Steel |
---|---|---|
Corrosion Resistance | Excellent | Poor (rusts) |
Weight | Light (1-2 lbs/ft) | Heavy (10-15 lbs/ft) |
Tensile Strength | High (70,000-100,000 psi) | Good (50,000-70,000 psi) |
Maintenance | Low | High |
Lifespan | 50-100 years | 20-50 years |
Note: Values vary by specific formulations and conditions.
FRP composites dominate in corrosion resistance, weight, and maintenance, while holding their own in strength. Steel’s raw power is impressive, but composites win for overall performance.
Real-World Wins: Where FRP Shines
The proof is in the projects. FRP composites are outpacing steel in:
- Bridges: FRP rebar and beams extend lifespan in salty climates.
- Marine Structures: Composites resist corrosion in docks and piers.
- Industrial Plants: FRP withstands chemical exposure where steel fails.
- Seismic Retrofits: Lightweight FRP strengthens buildings without added load.
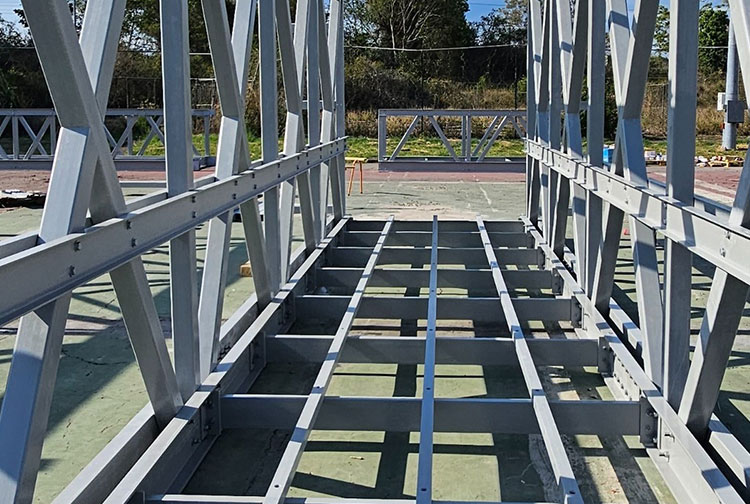
Caption: FRP composites enhance bridge durability in harsh conditions.
Reason 5: Versatility—Adapting to Any Challenge
Steel is rigid—literally and figuratively. It’s great for standard applications but lacks flexibility in design. FRP composites, however, can be molded into any shape—tubes, sheets, or custom profiles—and tailored with specific fibers or resins for strength, flexibility, or insulation. Need a non-conductive material for an electrical plant? FRP’s got it. Steel can’t compete with that adaptability.
Environmental Edge: A Sustainable Bonus
Sustainability matters, and FRP composites have an edge. Steel production pumps out CO2, while FRP’s longer lifespan and lower maintenance reduce waste and energy use over time. Though manufacturing composites isn’t carbon-free, their durability makes them a greener choice for eco-conscious projects.
Steel’s Last Stand: Where It Still Shines
Steel isn’t obsolete. Its lower upfront cost and unmatched compressive strength keep it relevant for dry, heavy-load applications like deep foundations or indoor frames. FRP’s higher initial price and lower fire resistance (unless treated) are hurdles, but in most modern scenarios, composites overcome these challenges.
Conclusion: Composites Claim the Crown
In the showdown of FRP composites vs. steel, Fiber Reinforced Polymers come out on top. Their corrosion resistance, lightweight strength, low maintenance, cost efficiency, and versatility make them a superior choice for today’s construction demands. Steel built the past, but FRP composites are building the future—longer-lasting, smarter, and more adaptable.
Why do composites win? Because they solve problems steel can’t, from rust to weight to upkeep. Ready to rethink your next build? Explore how FRP composites can elevate your project—or dive deeper into the world of advanced materials!