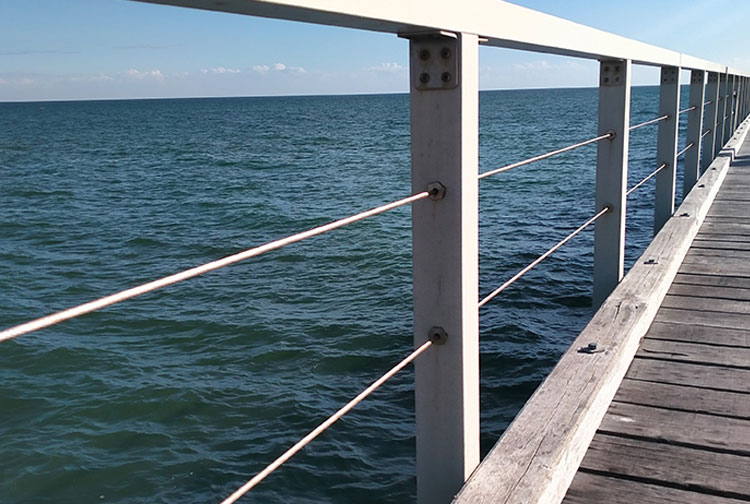
aption: FRP railings outlast steel in corrosive coastal environments.
Introduction: The Clash of Titans
In the world of construction and engineering, two materials have long battled for supremacy: steel, the time-tested giant, and fiberglass reinforced plastic (FRP), the rising challenger. Steel has built empires—bridges, skyscrapers, and ships—while FRP, with its innovative composite design, is carving out a new legacy. In this ultimate showdown of fiberglass reinforced plastic vs. steel, we’re pitting these titans head-to-head to see who comes out on top. Spoiler alert: FRP might just steal the crown.
Why does this showdown matter? Because choosing the right material can make or break a project—impacting cost, durability, and performance. From corrosion resistance to weight, strength to sustainability, FRP and steel bring different strengths to the table. Whether you’re a builder, designer, or industry enthusiast, let’s dive into this epic clash and uncover the winner.
The Contenders: Defining the Players
First, let’s meet our fighters. Steel is an alloy of iron and carbon, often enhanced with elements like chromium or nickel for added properties. It’s heavy, strong, and versatile, making it a staple in beams, rebar, and structural frames. Steel’s legacy is undeniable, but it’s not invincible.
Fiberglass Reinforced Plastic (FRP), also known as glass-reinforced plastic, is a composite material. It combines a polymer matrix—typically polyester, epoxy, or vinyl ester—with glass fibers for reinforcement. Available in sheets, bars, tubes, and custom shapes, FRP is lightweight, corrosion-resistant, and engineered for modern demands. With the contenders introduced, let’s step into the ring.
Round 1: Corrosion Resistance—Steel’s Weak Spot
Corrosion is the first punch in this showdown, and it’s a doozy. Steel is tough, with tensile strength ranging from 50,000 to 70,000 psi, but it rusts when exposed to moisture, salt, or chemicals. Rust doesn’t just mar steel’s surface—it weakens it, expands, and cracks surrounding materials like concrete. In harsh environments—coastal bridges, marine docks, or industrial plants—steel might need repairs or replacement within 20-30 years.
Fiberglass Reinforced Plastic lands a knockout blow here. Being non-metallic, FRP doesn’t rust, rot, or corrode, even in the toughest conditions. Studies show FRP can endure 50-100 years in aggressive settings, shrugging off saltwater, acids, and UV rays. A steel railing by the sea might crumble, while an FRP version stands firm. In the corrosion round, FRP takes the win.

Caption: FRP stands tall while steel rusts away in harsh conditions.
Round 2: Weight—Heavyweight vs Featherweight
Next up: weight. Steel is a heavyweight contender, clocking in at 490 pounds per cubic foot. That heft means more fuel to transport, bigger cranes to lift, and larger crews to install. For a skyscraper frame or bridge beam, steel’s bulk can slow projects down and inflate costs.
Fiberglass Reinforced Plastic is the featherweight champ, weighing just 1-2 pounds per foot—up to 80% lighter than steel. Yet, it’s no pushover, with tensile strength rivaling or exceeding steel’s at 70,000-100,000 psi. This lightweight strength makes FRP a breeze to handle, cutting installation time and equipment needs. For a rooftop structure, FRP wins this round with ease and efficiency.
Round 3: Strength—Power vs Precision
Strength is where steel flexes its muscles. Its compressive strength—up to 60,000 psi—makes it ideal for heavy loads, like deep foundations or massive columns. Steel’s durability under pressure has built cities, and it’s not stepping aside easily.
But FRP counters with precision. While its compressive strength is lower, its tensile strength shines, often doubling steel’s in tension-heavy applications like beams or cables. Plus, FRP’s strength-to-weight ratio is unmatched—delivering power without the bulk. In a bridge retrofit, FRP reinforces without adding load, while steel piles it on. This round’s a tie—steel for raw force, FRP for smart strength.
Round 4: Maintenance—Work vs Worry-Free
Steel demands upkeep. Rust-proofing, painting, and inspections are routine, especially in wet or salty climates. A steel bridge might need recoating every 5-10 years, costing thousands in labor and materials. Skip maintenance, and you’re gambling with safety.
Fiberglass Reinforced Plastic plays a different game—it’s virtually maintenance-free. No rust means no coatings, and its resistance to weathering and chemicals keeps it pristine for decades. Install FRP, and forget it—that’s a win for time and budget. In the maintenance round, FRP knocks steel out cold.
Round 5: Cost—Upfront vs Lifetime
Steel lands a jab with its upfront cost—$500-$800 per ton is hard to beat. FRP starts higher, at $1,000-$2,000 per unit, which can sting initial budgets. But the fight shifts over time. Steel’s maintenance and replacement costs pile up—think $50-$100 per beam annually—while FRP’s longevity slashes lifecycle expenses. Over 50 years, FRP could save 20-40% in harsh environments. Steel wins short-term, but FRP takes the long-term purse.
The Scorecard: FRP vs. Steel in Numbers
Let’s tally the rounds with hard data:
Property | Fiberglass Reinforced Plastic | Steel |
---|---|---|
Corrosion Resistance | Excellent | Poor (rusts) |
Weight | Light (1-2 lbs/ft) | Heavy (10-15 lbs/ft) |
Tensile Strength | High (70,000-100,000 psi) | Good (50,000-70,000 psi) |
Maintenance | Low | High |
Lifespan | 50-100 years | 20-50 years |
Note: Values vary by formulation and conditions.
FRP dominates in corrosion, weight, and maintenance, while steel holds ground in raw strength and initial cost. But the scales tip toward FRP for overall versatility.
Real-World Rings: Where FRP Triumphs
The showdown plays out in real projects:
- Marine Docks: FRP resists saltwater where steel rusts.
- Bridges: FRP rebar extends life in coastal climates.
- Chemical Plants: FRP withstands acids steel can’t.
- Railings: FRP offers lightweight durability by the sea.
Round 6: Versatility—FRP’s Wild Card
Steel’s rigid—great for standard builds but limited in flexibility. FRP adapts—molded into tubes, sheets, or custom shapes, and tuned with fibers for specific needs. Non-conductive and heat-resistant options make it ideal for electrical or industrial uses. Steel can’t match that range—FRP wins this bonus round.
Environmental Jab: A Green Edge
Sustainability adds a twist. Steel’s production is carbon-heavy, while FRP’s longer life and lower upkeep reduce waste. It’s not perfect, but FRP lands a green punch in eco-friendly projects.
Steel’s Defense: Where It Holds Strong
Steel fights back with affordability and compressive strength, shining in dry, heavy-load scenarios like indoor frames. FRP’s higher cost and lower fire resistance (unless treated) are weak spots, but they rarely sway the overall bout.
Conclusion: FRP Claims Victory
In the ultimate showdown of fiberglass reinforced plastic vs. steel, FRP emerges as the champ. Its corrosion resistance, lightweight strength, low maintenance, long-term value, and versatility outclass steel in most modern applications. Steel built the past, but FRP is shaping the future—smarter, tougher, and built to last.
Ready for the next round? Explore how FRP can transform your project—or dig into more material matchups to stay ahead in the game!